Conveyors - Full Listings
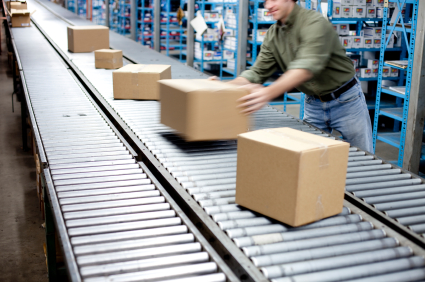
To implement a successful material handling solution, you must first be able to
describe and discuss the following factors:
- What problem do you have?
- What do you want to accomplish?
- What's your budget?
Also, additional factors must be realized before finalization of the project is complete. However, below are a few basic— but essential—facts that must be known and discussed when reviewing the improvement of your current operational processes. The essence of good design is this: have an idea. Know your load, your needs, your environment, deadlines and expectations.
1) Know your load
To properly apply the correct conveyor, the exact product and/or product mix must be discussed. A ‘box' will lead to more problems than ever expect to create a solution.
- What are your product(s) sizes and weights?
- If they are bagged, what is the product contained within the bag? Is it uniform?
- Is the product evenly distributed within the transport container?
- What is the color of the packaging of the carrying container? Some electronic scanning and applying devices today cannot read certain materials which can cause huge problems when start-up occurs!
- Is the product liquid, which can shift during transport?
- Are you using totes?
- Do they need bar codes or RFID tags?
2) Get familiar with your expectations
Make sure when discussing your project and application that you let us know what you expect to get from the new conveyor. If your expectations and hopes are clearly understood, the conveyor specification can be tailored exactly to your most pressing business needs. Some examples might include:
- Do you want to speed up production to shipping by 50%?
- Add floor space or increase storage capacity?
- Reduce your labor force?
- Make your work place more ergonomic?
- Reduce maintenance issues with existing equipment by replacing it?
- Conveyor system that utilizes PLC computer analytics?
- Reduce energy use, or increase plant sustainability?
3) Understand your working environment
All machinery is affected by its environment, and conveyor is no exception.
It is vital to understand at the start whether or not the operation will require conveyors of specialized construction, extra guards, different motors, or other adaptations to ensure that it can operate correctly in its environment.
- Do you have a dusty or dirty environment?
- Will oil, water or liquid spray or spillage on the product conveyed or around any of the equipment? Even the slightest possibility of this must be discussed
- Could there be heavy workforce interaction, shock loading, and fork truck traffic?
- Will the conveyor be installed overhead, creating a possible danger to those working under it in worst-case scenarios?
4) Know your required timeline from the very start
This is a fact that very often is discussed as the bid is finalized, and that is a formula for disappointment. It is easier to work backward from your completion date than it is to try to squeeze it in too late. Some conveyors can be shipped in as little as a couple of days under normal circumstances. Other models require more time to manufacture. Larger quantities, color options, or other modifications may also add lead time. It's best to have
provide your integrator with your deadlines as early as possible.
- Discuss the ultimate timeline for completion of the entire project regardless of different sectors involved.
- If it is a new building, are weather / construction allowances made for delays?
- Are all parties (robotics, controls, mezzanine, installers, general contractors, etc...) aware of your deadline?
5) Know what you will do once the conveyor is installed
- Do you have a training program for employees on the new equipment?
- Is maintenance training performed prior to the implementation of the conveyor system?
- Do you have a preventative maintenance contract or plan?
- Will you be tracking daily, weekly, monthly product throughput as compared to expectations?