Safer operations are more effective operations
Inadequate workplace safety in industrial facilities is a drain of time, money and resources. The best programs combine safety training, process improvements, a culture of safety and the right equipment and technology solutions to drive improvement. The good news is that safety improvements tend to more than pay for themselves. First, they can reduce potentially disastrous costs of a serious injury or fatality. Secondly, better safety tends to lift morale and create a better working environment. This improves productivity across the line and increases employee loyalty.
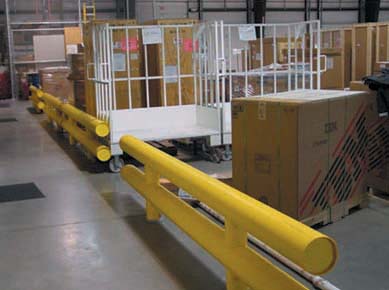
The tools and systems we offer tend toward storage and handling systems. Some safety areas, such as improving conveyor safety, utilize process and equipment modifications to reduce the chances of an accident. Others are "passive", such as safety netting or panels that help prevent inventory falling from high racks or overhead storage. Material handling equipment such as lifts, hoists and stackers help reduce the ergonomic impact of employees stretching or bending to lift heavy loads.
One of the best areas to focus on is forklifts - which tend to be the most dangerous piece of machinery in any operation that utilizes them. How bad is it? Forklifts produce just 1% of all industrial accidents, but 10% of all injuries in the space. That's why we focus on systems that help manage forklift/pedestrian traffic, reduce the mingling of people and forklifts, and generally work to warn and separate the two. Simple steel guard rail is one good way, but there are also warning sensors and automated gates for many applications.
Call us today as you plan your safety program - we will consult with you and help design ways to protect your employees from potential hazards.