The Wonder of Robotic Palletizing
Imagine filling a pallet in less than 3 minutes and having all layers interlocked precisely
I recently attended an ESOP event at a specialty paints and stains company. During the tour of their plant, I got to see a robotic palletizing system in operation. I was impressed. Standing about 6 to 8 feet away from the action, I watched as it placed 5-gallon cans of paint in rows of 3 stacked 3 high. Each row was offset from the previous one, so that optimum pallet space was used. As the robot picked up cans off the conveyor belt using a vacuum end effector, it placed them precisely on the pallet. Then, it slightly dropped down and “bumped” them to make sure they seated onto the row below. That action made me chuckle as I considered what a profoundly human act that was – a little hip action to make sure the cans seated correctly.
No breaks, no tired workers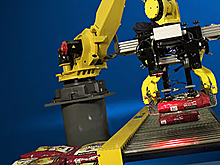
What impressed me was how quickly the entire pallet got loaded – less than 3 minutes without a single human touch. Each can was stacked atop the previous layer, 3 at a time. As pallets were filled, a forklift took them to the staging area or the warehouse. The robot even knew when to add a new pallet and re-start the process. And it worked consistently without taking a break or going to the water cooler.
I tried to visualize what it would take to do that job manually at that speed – a minimum of 3 strong men per shift who can stay out of each other’s way and still place the cans precisely. Imagine lugging a heavy 5-gallon can:
- … off the conveyor
- … over to the pallet
- … into a stacked position
– over and over and over again.
When you consider the hard labor moving a product at that speed takes and the ergonomic issues the workers suffer, you better be prepared to be hiring new people all the time. Moving heavy material manually at that rate creates a constant headache to hire and re-hire people to these types of demanding physical tasks. Just think of the ergonomics and loads involved – oh, my aching back!
It wasn’t ginormous either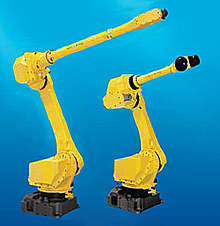
Yet this small robot (it probably stood about 8 feet tall and took up about 9 square feet of actual floor space) quietly, consistently made the job easy and effortless. Of course, its reach was much wider, probably close to a diameter of about 8-10 feet, but what it could do in that amount of space – it picked pallets up, placed them, picked up cans from a different spot and accurately placed them on the pallet. When a pallet was full, the robot pulled to a neutral position and waited until the pallet was removed. As soon as the space was clear, it kicked back into motion and started back at the routine. It was just too cool to be able to observe this palletizing system at close range.
Not where you’d expect to find robotics in use
The other thing that impressed me was that this was not at some gigantic manufacturing facility. It was a moderately sized operation in west-central Oklahoma. Somewhere you sure don’t expect to see a robotic application like that.
 More on robotic automation
Tags: ergonomics, Robotics, Time-savings, lean manufacturing, industrial safety, palletizing
Scott Stone is Cisco-Eagle's Vice President of Marketing with 35 years of experience in material handling, warehousing and industrial operations. His work is published in multiple industry journals an websites on a variety of warehousing topics. He writes about automation, warehousing, safety, manufacturing and other areas of concern for industrial operations and those who operate them.