An Ergonomic Labor Strategy
Ergonomic principles keep your workforce safe and healthy, in more ways than one
As we’ve discussed previously, labor is hard to find these days – and it will get harder every year. Cultivating your labor pool eases the need (and high costs) of hiring, training and retaining workers. One of the best ways to do this is to optimize as much as possible for ergonomics.
As the saying goes, what you appreciate appreciates.
Ergonomics plays a key role in a labor strategy by making jobs more attractive, helping workers get the work done faster and protecting them from chronic injuries. To help you outline a strategy for using ergonomics as a labor retention tool, here are a few standard ergonomics principles and how they affect labor.
1: Work at the right height
Working at the right height means making sure most of your movements are in the golden zone of mobility. This means workers don’t have to spend big chunks of time squatting, bending or reaching above their heads.
Portable ergonomic conveyors for trailer loading and unloading trucks are a great tool for putting this principle into practice. They use an adjustable height platforms to position workers at the best possible ergonomic work height. The conveyor itself tilts and pivots, so the conveyor can meet the products with minimal reaching and stretching by the worker.
These systems are estimated to cut the amount of labor-time in loading or unloading by about half. They also make the work easier on the people doing it, so it’s a win-win: you need fewer people to load or unload trucks and are more easily able to retain the workers you have in-house today.
How this principle optimizes the labor pool:
Reduction of time: When workers move less, they can do a job more quickly.
Minimizing injuries: Excess or awkward reaching creates chronic injuries. By not reducing the need to reach for things, you help keep your workforce healthy and reduce time lost to injuries and incidents. People are fresher, positioned better and make fewer errors as well.
2: Reduce excessive force
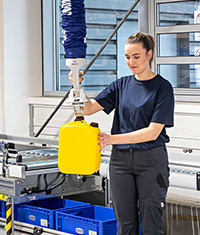
Reducing excessive force minimizes worker strain. This means designing the job so that employees don’t have to use their body weight to move a product through a process. Fortunately, there’s a lot of assistive technology out there to help accomplish this.
Lift-assist devices come in a variety of options, from lift tables to air balancers to vacuum lifters. Powered carts can allow workers to move heavy or bulky items across distances without strain. Conveyor systems and AGVs can transport heavy objects, rather than relying on manual and muscle-based transport.
How this principle supports labor:
Job attractiveness: Some roles don’t attract workers, because they’re difficult and come with muscle strain and pain. Making those jobs easier minimizes the discomfort involved, which gives you a better chance at keeping people in the role.
Wider labor pool: When a task requires less strength to perform, a greater number of people can perform it. In other words, you can hire a wider range of workers in terms of size and physical strength, which gives you a bigger talent pool to draw from.
What if you could offer the same job to smaller, older or less robust people? That’s a competitive advantage you can leverage.
3: Reduce unnecessary motions
The main goal of this ergonomic principle is to minimize the kind of repetitive motions that often contribute to musculoskeletal disorders (or MSDs). The tissue around our joints is tender, and when we repeat the same movements over and over throughout days, weeks and months, injuries can occur. By keeping motions limited to what’s strictly necessary, we lessen the chances of those injuries.
For example, sliding an object usually requires fewer motions than picking it up and putting it down. Designing a work process around sliding rather than requiring workers to pick work pieces up and move them to another area can minimize unnecessary motion. Ball transfers and rollers are great for this.
Another tactic is to examine the work surfaces your employees use.
- Are your surfaces larger than they really need to be? Or large enough?
- Do these surfaces require bending or stretching to reach supplies?
- Keeping them right-sized minimizes the amount your workers have to reach and stretch.
- Does the positioning require workers to move around to accomplish tasks? If so, is it possible to rotate or position order containers or components to reduce that movement?
How this principle supports labor:
Time savings: Workers can get more done in less time if they walk or move less, which helps you maximize your labor-hours.
Read more: The Ergonomics of AutomationÂ
4: Keep tools, loads and supplies within easy reach
Reaching isn’t productive, so minimize it.
You don’t want workers leaning far over a surface to reach something they need (especially if they’re reaching over mechanized equipment). Long reaches compound the risk of injury when workers have to move an object, and multiplied over time, they increase cycle time. This is an issue particularly as loads are heavier, bulkier, and require more handling.
Minimizing reach is usually a matter of focused design. Specialized organizational tools can make workstations fit the worker better, which means they won’t have to stretch and reach for the items they need. You can also use tilt tables or drop-door containers to allow easy quick and access to materials.
How this principle optimizes labor:
Injury prevention: Reaching long increases the strain on a human body when lifting or moving something, so keeping movements within the Golden Zone as much as possible can help keep your workforce healthy.
Time savings: You probably train your workers to use stools or ladders rather than attempt an unsafe reach, and this is an important practice. But the more often they have to do it, the more time each task takes (and the more likely they are to try to get by without the ladder). By keeping as many of the most necessary items as possible within easy reach, you can make your processes more time efficient.
5: Cognitive ergonomics
Besides the well-established ergonomic principles that focus on physical movements, our friends at Bostontec recently pointed out the benefits of minimizing mental movements as well. This field of study looks at things like memory, decision-making and problem-solving to create user-friendly systems that reduce mental workload.
This principle is at work in what we call goods-to-picker technologies like a VLM or AS/RS. These systems bring needed products to the order picker, rather than requiring the worker to walk to each item. This saves them the mental task of finding the location for the products on their pick ticket.
We’ve also found that systems like pick-to-light decrease the cognitive strain of picking, and as a side effect, companies have a deeper labor pool, because they don’t have to worry as much about reading skills or language barriers.
How this principle supports labor:
Besides expanding the pool of available labor, cognitive ergonomic optimization can make tasks more efficient—and therefore faster and less time intensive. It can also improve safety by reducing the risks of mistakes and accidents caused by misunderstanding.
Finding workers requires a multi-pronged strategy. Ergonomics is just a part of that strategy, but can be critically important in a competitive labor market. Employees care about their comfort and support at work – and tend to stay with companies who stress those needs longer than more difficult competitors.
Download our guide to workstations
Our guide to workstations features insights on ergonomic reach zones and how to lay out and organize stations for assembly, packing and more.
Download the guide today
Jessica Haring