Storage & Handling: How to Prevent Falling Items
In a warehouse operation, falling inventory is a persistent safety and inventory problem, but you can reduce the risks
What goes up…
In warehousing and storage operations where inventory is stored high on racks, stacked on floors, slotted into on multi-level shelving, mezzanine deck-overs or on suspended/overhead conveyor as it moves, there is one constant: things will fall. They fall because they’re stacked wrong. They fall because an order picker or a forklift bumps them. Things fall due to seismic activity, machine stops, or silly mistakes. Sometimes it seems like they fall for no reason at all.
What can you do to “stop the drop”?
Note: this article does not address falling items and seismic activity, but we have a comprehensive guide to warehousing in a seismic zone here. Check it out.
Storage racks and falling items
Let’s start with pallet rack since it’s so very common and the risks of falling items is greater from racks than just about any other place. First, since racks tend to contain very heavy items and full pallets, the weight of a fallen item can be dangerous. Pallet racks in particular suffer from this because they are tall by design — some are over 30′ tall at the highest beam level. Most anything falling from that height is going to not only be destroyed, but becomes a low-grade bomb that can injure people and break things when it lands. What steps can you take to reduce falling item risks when it comes to pallet racks?
1) Load racks with product drops in mind
A great many rack collapses and instances of falling items have to do with the way the rack was loaded in the first place. Without spending a dime, you can make a huge difference by simply loading the rack the way it was intended to be loaded.
Make sure your lateral pallet spacing is right: If your pallets are too close together, it’s harder to access them with a forklift. This increases the likelihood that a driver will make a mistake and bump an adjacent pallet, sending it to the floor. The industry standard is that your beam width (side-to-side) should be greater than your maximum total load width plus 12″. In a scenario of two pallets with a maximum width (including their loads) of 42″ each, you’d need a beam of at least 96″ wide (2 x 46 = 84″ + 12″ = 96″). That provides 3″ on each side and 6″ between the pallets. Don’t skimp on that extra lateral space. It helps prevent your drivers from knocking a load, a pallet, or even an entire rack down. National fire codes require a minimum 6″ flue space between loads. That should be the very minimum. See “Fire Code Compliance and Pallet Racks” for more information.
Provide plenty of vertical space, too: When it comes to space between beams, it’s important to regulate the overall height of your loads vs. the beam spacing in your rack system. The industry recommends that you should have a minimum of no less than 10 inches. Leave your drivers plenty of space to maneuver pallets as they load and unload. If your inventory mix changes, be sure your new pallets don’t exceed your beam spacing, and don’t allow the 10″ cushion to be compromised.
Light your warehouse: Dark conditions contribute to errors, and errors can result in a bunch of expensive inventory on the floor. Although rack aisles are notoriously difficult to light, modern lighting systems tend to be offset by energy savings and tax credits.
Store the heaviest items in the lower bays or on the floor level: This is common sense, but in a rack where there is a mixture of loads (say, bottled water and pillows), store the high density, heavy stuff on the ground and the pillows at the highest levels. This helps make your rack more stable and makes load/unload errors at the top less critical.
Train for better outcomes: If your drivers are loading expensive inventory, it’s a process to ensure it’s being done the way you want. You should have a specific process for loading/unloading to help reduce the chances of falling items. When you do forklift training, break down the various processes (how to deal with pedestrian crossings? How fast should I drive? How do I enter and depart truck trailers?). One of the written processes should be, “how do I load and unload racks?”
Load your racks evenly, with the loads centered. Many racks have wire deck or pallet supports that help them take nonstandard or undersized pallets. This is helpful, but if you misapply the load, loads can fall.The center of gravity for your pallets should not be focused on the front part of the beam level, as this pulls the rack forward. Some helpful articles on this include: “A Guide to Rack Load Types”, “When Racks Collide”, and “Pallet Rack Beams are Affected by Loading Patterns”.
2) Take care of your racks
- Inspect your racks regularly: See “A Guide to Pallet Rack Inspections” for more information. Be sure there are no bent frames, no missing beam clips, no hardware out of place. This should be done frequently and consistently.
- Report all incidents: Make sure people report any rack collision, even if there isn’t any apparent damage. Many companies make these collisions “no fault” to ensure that drivers can report them without fear of reprisal. You want to know as soon as you can if an upright has been compromised.
- Specify the right rack: If you are in a seismic zone, be sure to adhere to comply with regulations. We have an online guide for this, but you should always consult a rack professional if you’re erecting a rack system in an earthquake zone.
- Post your capacities: Label systems are inexpensive and easy to apply. Be sure that you get assistance if you change the storage mix, as pallet rack capacities are dependent on beam spacing. establish processes to be sure racks aren’t loaded with new items without checking their size/capacity beforehand.
3) Guard your rack’s worst fall points
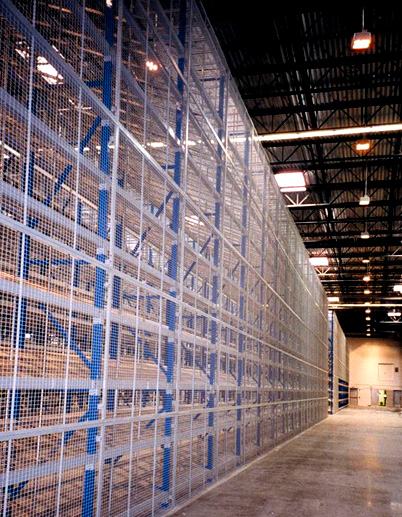
These safety measures are commonly used, relatively inexpensive, and deliver return-on-investment both in the product damage and safety arenas. You should install fall protection on high bays that overlook any work or traffic area, due to employee safety concerns. High value inventory, or areas that are frequently accessed by lift trucks also warrant protection.
Even a small carton that’s knocked off a pick bay from 20+ feet high can pack a punch when it hits the ground, or some unfortunate person below. Aside from that, of course, the inventory is damaged or destroyed.
- Rack safety nets: These nets are flexible and can help catch a carton if it’s inadvertently knocked off a stored pallet. In some cases, they can help prevent a mis-loaded pallet from pushing through the back of the rack and spilling onto the floor. Nets can be installed in dozens of standard and nearly unlimited custom configurations. They’re rated for loads weighing from 1,250 lbs. to 10,000 pounds. You can install them flat or offset to the back of a rack.
- Wire mesh back panels: These serve the same general purpose as netting, but are more substantial. They will not flex to catch a falling box, but instead are rigid and stop it from sliding past a certain point off the back of a rack storage position. They’re built from 2″ x 2″, 10-gauge welded wire mesh and securely welded into a 1-1/4″ x 1-1/4″ x 1/8″ angle frame.
For more information on using these tools, see “Comparing Pallet Rack Guards”, which examines the differences and which might work for your situation.
Help drivers to reduce damage as they load and unload racks with forklift lasers
Improve visibility as stored loads are accessed: One excellent new tool that helps drivers load a rack is the forklift positioning laser. These systems align with the fork tines and shine on the pallet in front of the forklift, providing a guideline showing the forklift operator the position of the tines at all times. Be sure the lifts don’t have solid tops or other impediments to visual inspection as they access your pallets.
Shelving and falling items
What are some steps you can take?
- Give your items some breathing room: One of the easiest ways to knock something off a shelf is to have too many items stored on one. Everyone who has worked in order picking probably can cite an incident where grabbing a stored box or bin pulled the one beside it off. That happens due to proximity; an edge catches on an edge. This may eat more floor space and require more shelves, but if you have the are to work in, it helps.
- Slot difficult items in the “golden zone”. Retailers store their most profitable, most purchased items in the mid range, eye-level, easily-reached shelf levels in part due to increase sales, but also for ergonomic and accessibility reasons. You should do the same in your product slotting scheme. Putting the things most needed on shelves where it’s easier to get them means your pickers will not be reaching or stretching as often, which means they won’t drop it as often — or knock an adjacent product off the shelf.
- Shelf-supported mezzanines present special challenges: An order picker can easily push a stored item through to the other side, where it can fall to the floor level, which can result in product damage and some danger to workers on the other side. To alleviate this, use closed back shelving units or install safety nets on the outside of your shelving.
- Don’t overload and don’t mis-load: Shelving, like rack, can collapse and spill its load if it isn’t properly loaded. Take care to be sure you don’t exceed either the shelf level or total unit capacities. Also, be sure your loads evenly distribute the weight across an entire shelf.
Conveyors and falling item prevention
In many facilities, conveyors are installed overhead or suspended from the ceiling to help conserve floor space. This can and does elevate loads and creates a potential fall hazard as product is conveyed above the floor. Loads can also fall from inclined conveyors as they are conveyed up or down. Even on a floor mounted conveyor a spill can split a case, land on an order pickers’ toes, or damage inventory.
OSHA 1926.555 (a) (5) states that: “Where a conveyor passes over work areas, aisles, or thoroughfares, suitable conveyor guards shall be provided to protect employees required to work below the conveyors.” That’s the reality. You have to guard conveyors over a work aisle, but you also need to consider it in other areas where safety isn’t the concern and product protection is. What are some steps you can take to reduce these risks?
Trough conveyor guards
These troughs help keep loads contained on the conveyor belt and prevent them from falling. Guardrail is built onto the frame forming to keep loads on track, creating the “trough” for handling loose parts or other loads that require guard railings. Seen above in a package handling operation with takeaway to a trash line. In some situations, bulk parts can be conveyed and protected with this method. Excellent for incline/decline, straight line operations. These can be specified in a range of sizes and angles.
Side mounted guard rails
For conveyors with packages, totes and other small loads, side mounted guard railing provides good protection against product spills. Ideal for curves, as these rails can track exactly to the shape of the conveyor as it moves through a facility.
Conveyor safety nets
In operations where conveyors pass overhead, it’s not unusual to see conveyors guarded by both side-mounted guard railing and conveyor system safety nets, to provide redundant safety. These systems help prevent falls that standard conveyor guardrails can’t, (falling conveyor components or large cartons that escape the limited reach of fixed guardrails). Nets will even catch a conveyor roller if one happens to fall. Nets can also be specified with a fine weave that catches smaller falling parts, hardware, etc. They provide flexibility in dealing with falling items that aren’t necessarily present in guardrail-based solutions.
Tags: product damage, conveyor safety, warehouse control, Inventory protection
Scott Stone is Cisco-Eagle's Vice President of Marketing with 35 years of experience in material handling, warehousing and industrial operations. His work is published in multiple industry journals an websites on a variety of warehousing topics. He writes about automation, warehousing, safety, manufacturing and other areas of concern for industrial operations and those who operate them.