How Dock Operations Improve Customer Service
The loading dock is the heart of the distribution center, touching most every inbound or outbound item
A loading dock is like a football center: It touches the ball every play, but gets no glory when things go well.
Almost all warehouses and manufacturing facilities induct and ship out almost everything through the dock area. Your shipping and receiving areas are the conduit between your operation and the world beyond. Finding ways to improve operations in the dock area can yield positive results for almost any business. Whether your operation processes 10 pallets or 10,000 packages a day, you can improve the entire operation by optimizing dock operations.
Don’t let dock & shipping areas become a bottleneck
- Loading efficiency: The faster a shipment is processed out, the better. In a busy situation, that trailer bay is waiting on the next truck, and more are lining up for the spot. Every moment spent waiting on trailer loading is lost time and productivity for both the distribution center and the truck lines. Good load sequencing is critical, as customers at the other end of the shipment want an organized trailer that’s efficient and safe to unload. The ability to quickly and accurately load a truck is a core competency for any warehouse operation.
- Unloading efficiency: Since trucks are loaded last-in, first-out, a plan to quickly and efficiently a variety of products is vital. Trucks are sometimes loaded with a mix of full pallets and parcels, the process of inducting these loads to correct warehouse storage positions can be a challenge. Sorting incoming shipments may mean breaking down pallets on the floor of a busy staging area and assigning them on the fly to storage positions. Sometimes, workers must enter a trailer and break a pallet down or retrieve items simply stacked on the floor, then hand-carry them out, which compounds the issues and increases labor consumption.
- Safety is a huge concern: As we have mentioned previously, docks are a big safety concern — perhaps the biggest in some warehouses — accounting for up to 25% of all warehouse injuries. Forklift/pedestrian accidents, trailer creep forklift falls, slip & fall accidents, trailer load shifts, worker dock-edge falls and more are possible. Finding ways to reduce labor at the dock not only saves money, but can cause a decrease in injuries and worker compensation claims. Typically, this involves increased ergonomics for the workers who remain in the process.
- Labor efficiency is the life’s blood of shipping/receiving: Whether shipping or receiving, docks consume labor like few other areas of a facility. This labor consumption isn’t always uniform, which compounds the issue. A dock can be still one moment and bustling the next.
Potential dock operation improvement concepts
Utilize telescopic or extending conveyors to increase loading/unloading efficiency
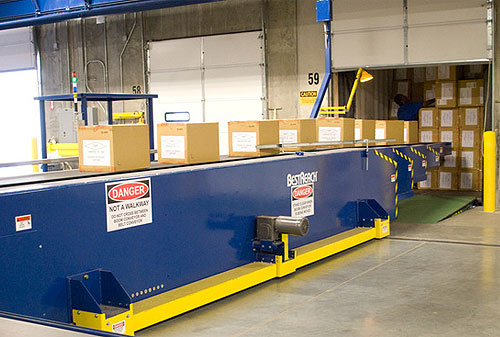
One of the most common gaps in a distribution center is that zone where orders travel through an automated conveyor system, then reach the dock area. There, they are often stacked onto pallets, rolled on carts, transported on pallet jacks, or even hand-carried to a waiting trailer. This gap has always vexed DC operators, as it interrupts smooth product flow and creates a bottleneck. Telescopic conveyors are a good solution. These conveyors allow you to eliminate the gap between a conveyor system and the dock by extending product flow all the way to the back of a waiting trailer. A warehouse worker stands in the trailer and processes finished orders right there.
Essentially, these conveyors let you extend your plant system into the trailer in a flexible, safe manner. Trucks are loaded and cubed better because your shipping workers are able to stack or break them down on the spot, with orders sequenced any way you want them. These systems create continuous product flow.
Not only does this create a more efficient loading experience, it reduces the need for forklifts in the zone, which means they can be at work elsewhere. That’s safer and more efficient. And since you eliminate an entire handling step, labor usage declines using these systems.
Increase dock area ergonomics
Docks are notoriously difficult work, and tired workers make more mistakes. Focusing on ergonomics reduces injuries and creates productivity. Ideas include:
- Make sure workstations are ergonomic. This means that if there are packing benches, conveyor workstations or other areas, be sure to minimize the reaching, bending, and stooping that can make them more difficult for workers. See A Quick Guide to Warehouse Ergonomics for detailed information.
- Let the air flow. Docks are notorious for fumes from trucks and forklifts. Ventilation panels in dock doors are one way to help bring more fresh air in, but you can also leave doors open with folding gates to restrict access, or mesh panels to reduce debris and insects and still accomplish the same thing. (Strip doors area also excellent for these applications.) Consider HVLS (high volume, low speed) fans for dock areas. They considerably improve the working environment.
- Increase lighting. Use efficient, bright lights overhead. Consider dock light arms to make sure the interior of trailers are adequately bright for workers.
- Seal the doors and dock pits adequately in winter to reduce cold.
Stretch wrap pallets faster and more effectively
Stretchwrapping results in far better, more stable pallets. Products are far less likely to shift, and pallets are more cohesive; you’ll suffer less freight damage and fewer returns. Good pallet construction the first line in customer service, but the manual stretchwrapping process can be labor intensive and ineffective. It’s also a potential bottleneck.
The consumption of wrap materials, the labor used, and the time it takes all contribute to the issue. But wrapping pallets is a vital function, as the stretch wrap can protect loads, help maintain pallet integrity, and even increase security. Automated stretch wrap systems aren’t suitable for every shipping operation, but are true productivity tools in the right situation.
Typically, wrapping pallets is labor intensive. Semiautomatic wrapping systems can integrate with conveyors or other automation equipment and reduce that labor usage. Fully automated systems require no labor at all. They wrap, cut and weigh the film down with no human intervention at all.
See: Stretch wrapper Justification & Specification for detailed information.
Actively engage safety issues
Because forklifts are used to load and unload so many trailers, special attention must be paid to safety considerations, both for the forklift driver and warehouse floor workers who coexist with them in the dock area. One critical area is the safety of pedestrians directly outside the trailer. Utilize inexpensive forklift “blue” safety lights to help warn them that a forklift is emerging from a dock area.
This does little to warn drivers, however, that pedestrians may be in harms’ way as they back out of a trailer. A variety of motion-based warning systems are available, and are both economical and easy to install that can help warn drivers with flashing lights and/or audible alerts that a pedestrian is in the zone.
Forklift blind spot camera systems for lower quality light situations can be connected to cameras mounted on the rear of a forklift that let the driver see what’s behind as she backs from a trailer. This creates more awareness in these difficult situations.
Falls are a significant issue at docks, both for forklifts and pedestrians.
Make sure trucks are adequately chocked, or restrained so that they cannot pull away or nudge away from a dock while a driver is loading/unloading the trailer. Provide secure driver lounges and enforce a disengagement process that ensures the truck doesn’t depart until you are ready. Paint the edges of dock boards bright yellow and increase lighting to ensure the driver can maneuver the forklift into the correct area.
For dock workers, train about the dangers of working near an edge. Install dock safety gates to help ensure that edges aren’t guarded.
See OSHA’s dock safety area for more information.
More information:
- Better Efficiency Begins at the Dock – Inbound Logistics
- How to Specify a Dock Lift – Cisco-Eagle
- How to Specify a Yard Ramp – Cisco-Eagle
- Security at the Loading Dock – Cisco-Eagle
Tags: customer service, labor, ROI
Scott Stone is Cisco-Eagle's Vice President of Marketing with 35 years of experience in material handling, warehousing and industrial operations. His work is published in multiple industry journals an websites on a variety of warehousing topics. He writes about automation, warehousing, safety, manufacturing and other areas of concern for industrial operations and those who operate them.